This article is sponsored by Realterm
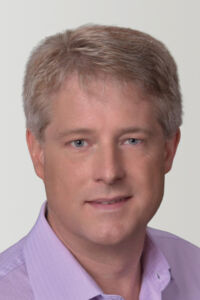
Global trade, e-commerce and technological changes in the transportation sector are fueling a growing need for industrial outdoor storage (IOS) properties where transportation equipment may be efficiently stored but frequently moved. IOS properties are one component of what Realterm describes as transportation logistics assets – the universe of mission-critical buildings with high flow through characteristics that are optimized for the movement of goods rather than for long-term storage.
The value of an IOS property lies in the utility to achieve transportation efficiency for the logistics user. These may include cross-dock truck terminals, drayage yards, intermodal yards, truckload drop lots, trucking fleet operations centers, delivery van parking facilities and other land-intensive secure storage uses that support the transportation industry in this highly varied and operationally complicated real estate subsector.
Realterm’s recent analysis examined several different types of users of IOS properties and identified the financial function that these properties play in generating cost savings and revenue enhancement for each. The analysis was based on a combination of empirical data provided by occupiers and hypothetical data derived from industry standards of practice.
The primary benefit of IOS properties to the occupier is in avoiding higher costs that may be incurred elsewhere in the supply chain, and the resulting financial benefit to the occupier is the primary driver of rent growth in the sector. The potential achievable rents for these properties are a function of the opportunity cost of not having access to these properties and the availability of competing properties. The IOS property types considered in this analysis included drayage yards, truckload drop lots and truck terminals.
In each of these cases, proximity between IOS properties and warehouses, seaports, inland ports, maintenance depots, rail terminals or individual consumers reduces fuel and labor costs and enables a higher “turn rate” for consumer goods. In logistics terms, stalled inventory is lost revenue to retailers.
In 2020, the most recent year data was fully available, global logistics spending totaled $6.5 trillion, according to logistics and supply chain market research firm Transport Intelligence. The combined logistics industries in the US and Europe accounted for approximately $2.8 trillion in economic activity, about half of the global total.
Spending on trucking is close to 70 percent of all domestic freight moved in both the US and Europe. The intersection between marine shipping and domestic trucking creates a heightened need for IOS properties to speed the transfer of goods between these two dominant transport modes.
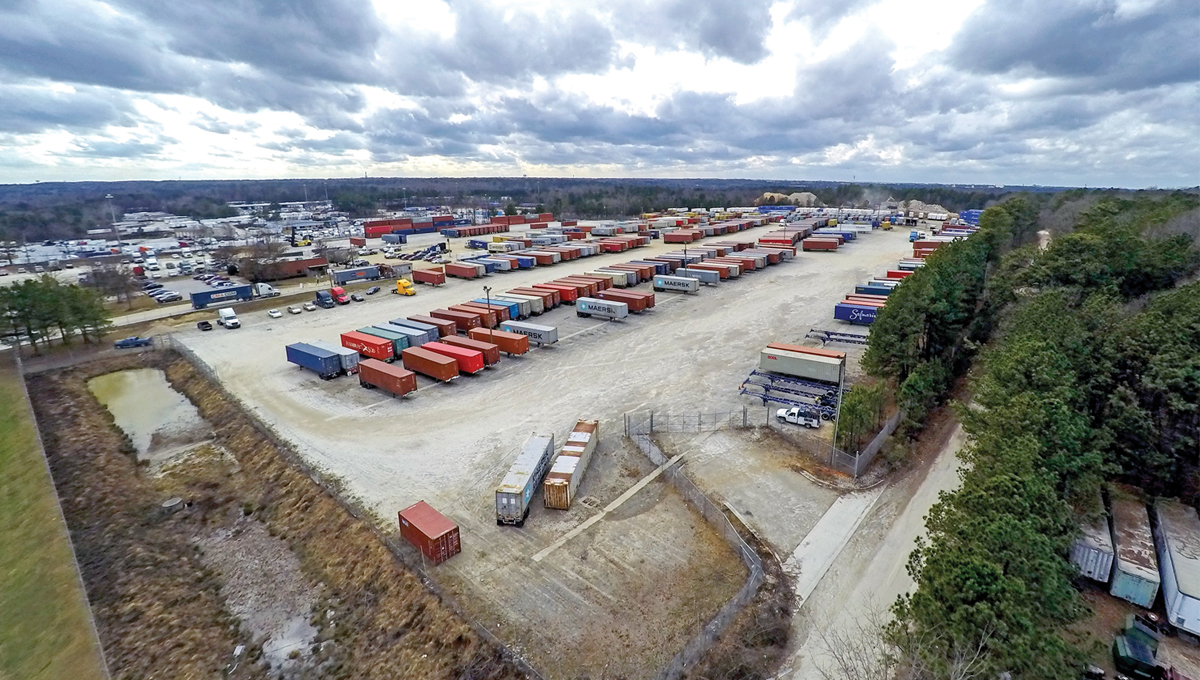
In addition, the rise of global e-commerce direct-to-consumer networks has heightened the need for these properties to store and queue last-mile delivery vehicles, among other uses. Over the past decade, online retail sales have increased by an annual rate of 11.2 percent in the US and 8.5 percent in Europe. Final-mile delivery costs can amount to as much as 70 percent of a logistics operator’s cost structure. The ability to minimize these final-mile costs is an essential driver of profitability for the user.
Drayage yard
Drayage is the movement of goods to and from a port or terminal. Drayage yards help shippers minimize the cost of these movements by shortening the time a container is in use and providing a port-proximate location where a container may be unloaded, then returned to the shipper.
To incentivize the rapid throughput of containers, ports often impose a per-container port storage fee. Shipping companies may pass this cost through to the beneficial cargo owner by levying a fee called demurrage when containers are not moved off the port within a specified time frame. In addition to a demurrage fee imposed while waiting for a container to be picked up, the shipping company may also impose a detention fee if the containers are not returned to the shipping company by the cargo owner within a specified time frame after the container has been moved off the port.
A drayage yard can help a user mitigate these costs. A location proximate to the port allows for more trips to be made by each driver from the port to the yard, resulting in fewer days that containers must spend at the port or away from it, thus lowering both demurrage and detention fees. At a heavily congested port, a shipper may not be willing to pay rent at an IOS facility that is higher than the combined cost of what would be otherwise charged for container demurrage and detention.
While there is likely an exceptionally high ceiling on what drayage users may be willing to pay in rent, the relative availability of functional competitive space can moderate rent growth in the sector. Nevertheless, the ongoing conversion of under-developed, industrially zoned land to warehouse use suggests that rent trends Realterm has observed in the IOS segment of the high flow through logistics sector over the past decade are sustainable, especially in markets with high barriers to entry and with carriers facing high regional transportation costs.
Truckload drop lot
Truckload drop lots allow a trailer to be filled and brought to a drop lot where it will be ready for a driver to pick up the load immediately after dropping off another load. The purpose of these drop lots is to capture full truckload economics, minimizing distances traveled with empty trailers as carriers move from one shipment to the next. These lots also help to minimize the number of unproductive hours in a driving shift that a driver is not moving freight.
Typically, drivers wait nearby while a trailer is loaded, which can often take up to several hours. These hours count against a driver’s hours-of-service limit, further restricting the availability of a driver to make additional deliveries. A drop lot allows a trailer to be filled and brought to a lot where it will be ready for a driver to pick up immediately after dropping off another load, decreasing driver down time. Another benefit of these lots is to provide flexibility in departure times for pre-loaded trailers to avoid heavy traffic.
Furthermore, drop lots are a means of minimizing the negative impact from the reduction in revenue from driving shorter distances. Truckload operators today are often required to make trips shorter than 350 miles, a distance below which transportation costs due to wait times and traffic congestion represent a significantly larger share of the driver’s hours of service.
Realterm’s analysis shows that the efficiency achieved by these facilities can represent a cost savings several times what occupiers may pay in rent.
Truck terminal
A fully loaded truck moving from its origination point to its destination point along the most direct route with no down time is the most efficient manner by which to move truck-carried freight. However, most trucks frequently carry just 30-50 percent of their capacity.
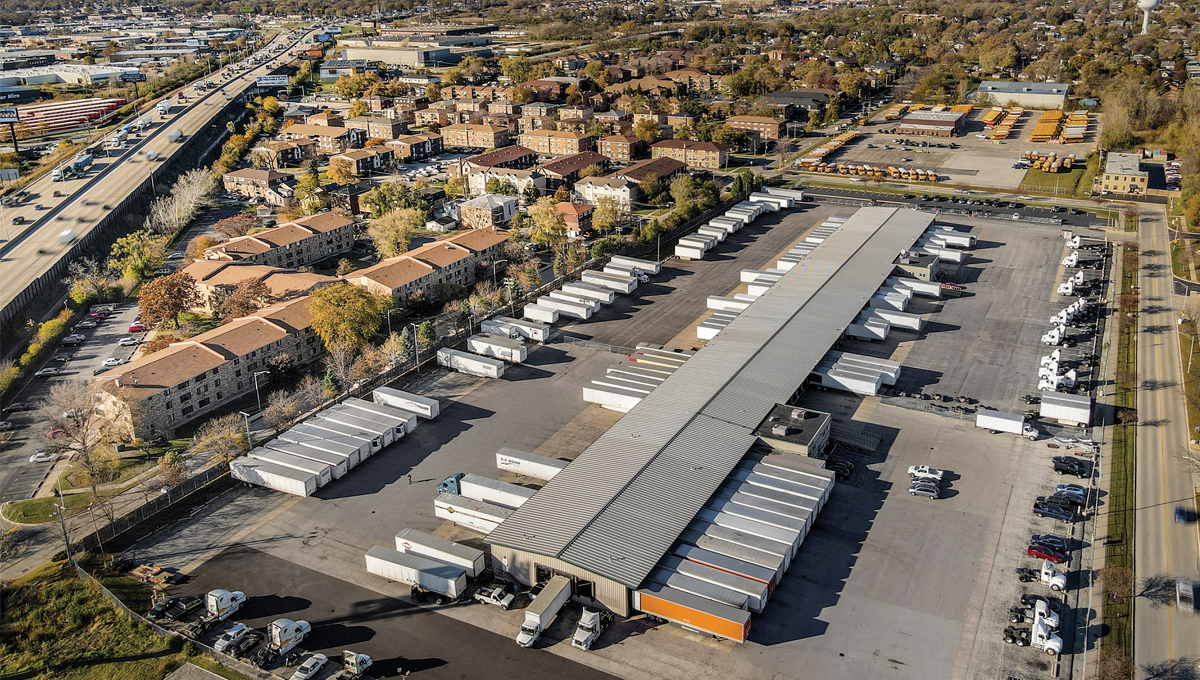
Less-than-truckload (LTL) carriers aggregate these smaller shipments, gathering freight along feeder routes, where shipments are consolidated at a truck terminal for long-distance travel. At the end of the long-distance route, shipments are then deconsolidated at another truck terminal for local delivery along last-mile distribution routes.
These “hub and spoke” networks can get even more complicated, with terminals handling consolidation and deconsolidation operations from multiple shippers for local delivery, or shipments routed through multiple destination terminals from the same shipper. The more complicated these networks become, and the more freight volume routed through a terminal, the more critical the timing of operations becomes.
The value of a truck terminal to an LTL carrier comes from the ability of the user to consolidate shipments and reduce transportation costs that would otherwise be incurred if each shipment were carried separately via truckload carrier. How much an occupier is willing to pay in rent for a given truck terminal is a function of the value of that specific property in generating cost savings to its operations, capped by the lowest rent available at competing terminals that could generate equivalent cost savings to the user.
Realterm’s value analysis illustrates that operating a delivery network of trucks in a way that maximizes the use of trailer volume per truck can yield considerable cost savings compared to using a single truck for each shipment.