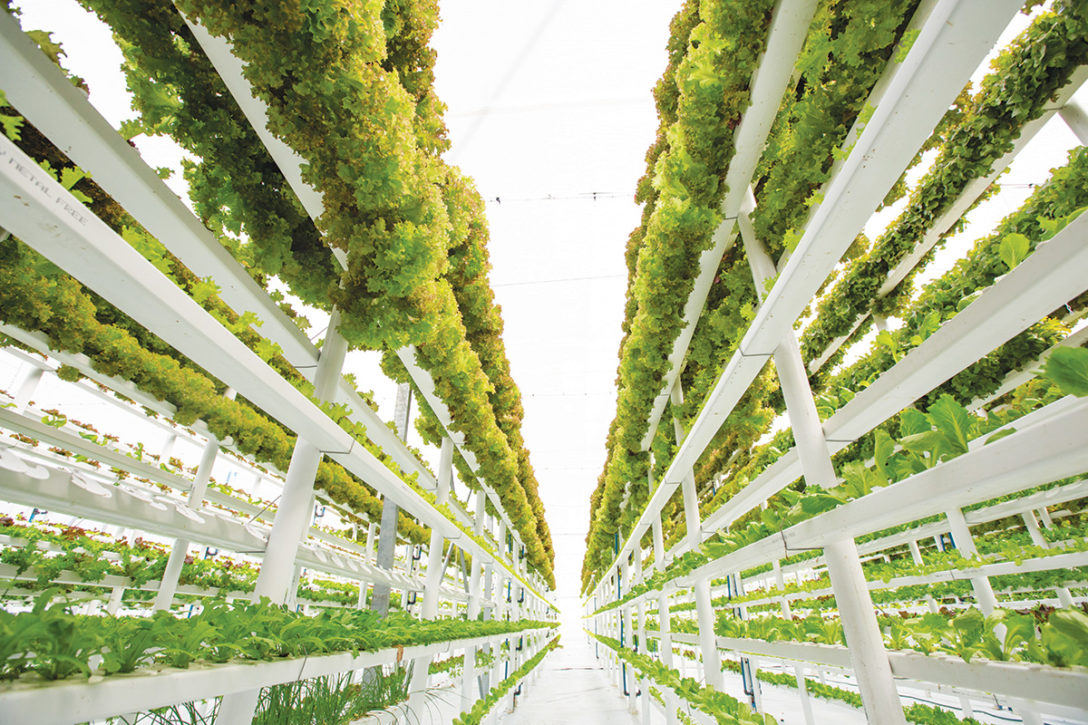
How farms fit into real estate portfolios amid deglobalization
Urban farming may be a niche business today, but its future growth potential is significant as food security issues increase.
Urban farming may be a niche business today, but its future growth potential is significant as food security issues increase.
Copyright PEI Media
Not for publication, email or dissemination